Got back into crawlers again, but scale now is way more advanced than before. Started with a TRX-4M. Didn't even finish off the battery before it was in pieces. It's a pretty nice little machine to be honest. It will be rebuild as somewhere between an overland style truck and a service truck. Will play nice with my 1:14 scale semi trucks and still technically "micro" in 1:14. Don't expect it to crawl great, but should look the part.
Body STL file was bought from Cults3D and scaled to 1:14. Pieces were combined to reduce print cost-- Slight fitment adjustments are needed
Taking half of a Meus Axle and half of the stock traxxas creates this chunk that holds all the bearings. Now i don't need to mess with cutting/printing bearing pockets. Clamp thickness will be tough to match on the axle body. Need to cinch down on the bearings just as the two halfs clamp to the axle housing. Going to be hand-fit.
I will order the purple part to link up the off the shelf parts. Short side axle shaft is stock -4M. Long side will need to be extended. Outer Cs and knuckles will be stock. Varius tabs from stainless steel sheet will be laser cut and welded on. Tubes are 5/16" OD .028" wall. Pretty close to a scale 4" axle tube. Ends will be turn down to press into the purple part. Some welds along the outside for good measure.
160" wheelbase in 1:14 scale. A bit of a trail limo. High CG thanks to the metal bed. STL of the body is huge in terms of file size. Had to reduce/omit to get it to show in CAD. Was printed at the original higher-mesh.
Weld teaser on .5mm stainless. Tray will be ~0.8mm with some 1.2mm here and there.
- TRX-4M bastard axles- stainless steel tubes and center section, Meus pinion mount/gears, stock diff cover/bearing support. Stock CV joits, axle C and Hubs. Construction will be tiny welds.
- Superduty SLA body
- Flatbed/Tray like the aussies use, but in stainless steel sheet
- Suspension: front might be ford-style radius arms in stainless steel. Rear will be stock -4M links
- Transmission unknown, maybe just a planetary gearbox and 1:1 transfer case
- Motor: HobbyWing mini16 - looks like i'll have to turn down the motor shaft to 2mm
- Wheels/tires: 65-70mm OD is slim pickings. RC4WD Lego series is my best option now. Ideally 1.2in wheels or so to be scale-ish. Wheel will likely be SLA printed since Meus stuff is too much offset
- Some blinky lights
- 2S lipo
- Jeti radio shared with all my toys
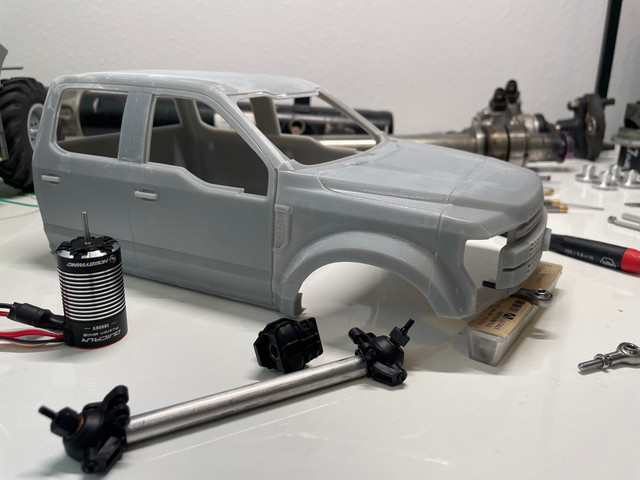
Body STL file was bought from Cults3D and scaled to 1:14. Pieces were combined to reduce print cost-- Slight fitment adjustments are needed

Taking half of a Meus Axle and half of the stock traxxas creates this chunk that holds all the bearings. Now i don't need to mess with cutting/printing bearing pockets. Clamp thickness will be tough to match on the axle body. Need to cinch down on the bearings just as the two halfs clamp to the axle housing. Going to be hand-fit.


I will order the purple part to link up the off the shelf parts. Short side axle shaft is stock -4M. Long side will need to be extended. Outer Cs and knuckles will be stock. Varius tabs from stainless steel sheet will be laser cut and welded on. Tubes are 5/16" OD .028" wall. Pretty close to a scale 4" axle tube. Ends will be turn down to press into the purple part. Some welds along the outside for good measure.


160" wheelbase in 1:14 scale. A bit of a trail limo. High CG thanks to the metal bed. STL of the body is huge in terms of file size. Had to reduce/omit to get it to show in CAD. Was printed at the original higher-mesh.

Weld teaser on .5mm stainless. Tray will be ~0.8mm with some 1.2mm here and there.